Understanding Deep Drawing vs Stamping
Deep drawing and stamping are two vital processes in metal forming, each with distinct characteristics and applications. While both involve shaping sheet metal, their methods and outcomes differ significantly.
Deep drawing focuses on creating seamless, deep parts through a series of incremental draws, making it ideal for cylindrical or complex hollow shapes. In contrast, stamping emphasizes cutting and forming flat metal sheets into various shapes and designs through techniques like blanking, embossing, and coining.
Both processes serve industries such as automotive, aerospace, and consumer goods, but their suitability depends on factors like material thickness, desired shape complexity, and production volume. By understanding their differences, manufacturers can choose the optimal method for their needs.
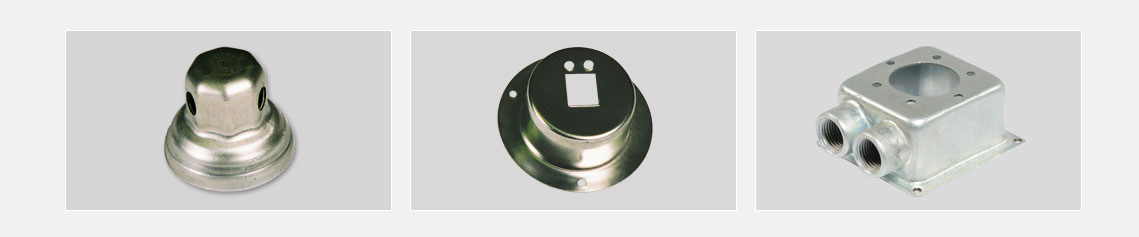
What is Deep Drawing?
Deep drawing is a metal forming process used to create intricate and seamless parts by transforming flat sheet metal into deep, hollow shapes. This process involves pressing a sheet of metal into a die with a punch, gradually drawing it into the desired shape. The defining characteristic of deep drawing is its ability to produce parts with depths exceeding their diameter, such as cylinders, cups, or even complex automotive components.
The process is conducted in multiple stages to prevent the material from tearing or wrinkling. It often involves lubricants to reduce friction and ensure smooth shaping. Metals like aluminum, stainless steel, and copper are commonly used for deep drawing due to their malleability and strength.
Deep drawing is favored for its ability to produce lightweight, strong, and durable components in large volumes. Its common applications include manufacturing fuel tanks, kitchen sinks, and aerospace parts, where precision and durability are crucial.
What is Stamping?
Stamping is a versatile metal forming process that involves cutting, shaping, and forming sheet metal into desired shapes using a die and a press. Unlike deep drawing, stamping primarily focuses on creating flat or slightly contoured parts through high-speed operations, making it ideal for mass production.
This process encompasses various methods, including:
- Blanking: Cutting out a specific shape from a sheet of metal.
- Embossing: Creating raised or recessed designs for aesthetic or functional purposes.
- Coining: Producing precise details by compressing the metal.
Stamping is often used to manufacture parts for industries like automotive, electronics, and appliances, where speed and precision are essential. Materials such as steel, aluminum, and brass are commonly utilized, chosen for their ability to withstand repeated high-pressure impacts without losing integrity.
The efficiency and cost-effectiveness of stamping make it a preferred choice for producing components like brackets, panels, and connectors. By enabling rapid production of uniform parts, stamping ensures consistency and scalability for large-scale manufacturing projects.
Comparing Deep Drawing and Stamping
Deep drawing and stamping are both essential metal forming techniques, but their applications and processes differ significantly. Here’s a closer look at how they compare:
Key Differences
- Complexity of Shapes:
- Deep Drawing: Ideal for creating deep, seamless, and hollow components, such as cylinders and cups.
- Stamping: Suited for flat or slightly contoured parts with intricate designs.
- Material Usage:
- Deep Drawing: Requires materials with high malleability to prevent tearing during the drawing process.
- Stamping: Can handle a broader range of materials, including harder metals, due to its high-pressure operations.
- Production Speed:
- Deep Drawing: Slower, as it involves multiple stages to ensure precision and prevent defects.
- Stamping: Faster, making it more suitable for high-volume production.
- Tooling Costs:
- Deep Drawing: Higher initial costs due to the complexity of dies and equipment.
- Stamping: Generally lower, especially for simpler designs.
Comparison Table
Before physical production, there may be instances where we need to create a virtual prototype or even physical prototype of the part, allowing us to simulate the entire deep drawing process. This helps identify and resolve potential design issues early, saving both time and resources.
Feature | Deep Drawing | Stamping |
---|---|---|
Depth of Parts | Deep, hollow shapes | Flat or contoured designs |
Production Speed | Moderate | High |
Tooling Costs | High | Moderate |
Material Types | Soft, malleable metals | Wide range, including hard metals |
Materials Used in Deep Drawing and Stamping
The choice of material plays a critical role in the success of both deep drawing and stamping processes. Each technique demands specific properties to ensure quality and efficiency in production.
Materials for Deep Drawing
Deep drawing requires materials that are ductile, malleable, and capable of withstanding deformation without cracking. Common materials include:
- Aluminum: Lightweight and corrosion-resistant, making it ideal for automotive and aerospace components.
- Stainless Steel: Offers durability and resistance to corrosion, frequently used for kitchen sinks and medical equipment.
- Copper: Known for its excellent conductivity, often used in electrical applications.
Materials for Stamping
Stamping accommodates a broader range of metals, including those with higher hardness levels, as the process primarily involves cutting and shaping. Common materials include:
- Steel: Preferred for its strength and versatility in automotive and construction applications.
- Brass: Combines aesthetic appeal with machinability, used for decorative and functional components.
- Titanium: Lightweight and highly durable, popular in aerospace and medical industries.
Material Selection Factors
- Thickness and Strength: Deep drawing typically uses thinner sheets, while stamping can handle thicker materials.
- Final Application: Parts requiring seamless construction may benefit from deep drawing, while stamping is better for flat or detailed shapes.
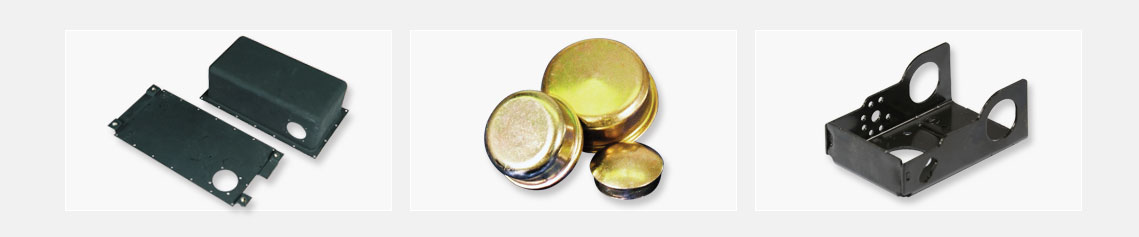
Benefits and Challenges of Each Process
Deep drawing and stamping each offer unique advantages and challenges that make them suited for different manufacturing needs. Understanding these aspects can help determine which process is best for specific projects.
Benefits of Deep Drawing
- Seamless Construction: Produces durable, one-piece components without joints or welds, ideal for high-pressure or fluid-tight applications.
- Material Efficiency: Minimizes material waste compared to other processes.
- Aesthetic Appeal: Creates smooth and uniform surfaces, suitable for visible parts like cookware and appliances.
Challenges of Deep Drawing
- Higher Tooling Costs: Initial costs for dies and equipment are higher, especially for complex shapes.
- Material Requirements: Limited to ductile metals, which may restrict material options.
- Slower Production Speeds: Multistage operations can take more time compared to stamping.
Benefits of Stamping
- High-Speed Production: Ideal for large-scale manufacturing of parts with consistent quality.
- Versatility: Accommodates a wider range of materials, including harder metals.
- Cost-Effective for Simple Parts: Lower tooling costs for straightforward designs.
Challenges of Stamping
- Limited Depth: Less suitable for deep or hollow parts.
- Potential Material Waste: Can produce more scrap compared to deep drawing.
- Surface Finish Variability: May require additional processing for high-precision or aesthetic requirements.
Applications Across Industries
Applications of Deep Drawing
Deep drawing is favored for creating seamless, durable components that require complex shapes and high precision. Common applications include:
- Automotive Industry: Fuel tanks, mufflers, and structural components.
- Aerospace Industry: Lightweight, hollow parts like engine casings and satellite components.
- Consumer Goods: Kitchen sinks, cookware, and electrical enclosures.
- Medical Equipment: Seamless containers and surgical instruments.
Applications of Stamping
Stamping excels in producing flat or moderately contoured parts at high speeds, making it a go-to process for mass production. Typical applications include:
- Electronics Industry: Connectors, brackets, and enclosures.
- Automotive Industry: Panels, brackets, and small intricate parts.
- Appliances: Control panels, decorative trims, and housings.
- Construction: Metal fasteners and structural components.
Deciding Between Deep Drawing and Stamping
Choosing between deep drawing and stamping requires evaluating factors such as part design, production volume, material suitability, and budget. Deep drawing is ideal for creating seamless, hollow components and is well-suited for projects requiring medium production volumes and precise designs. Stamping, on the other hand, excels in high-volume manufacturing of flat or moderately contoured parts, offering cost efficiency and versatility for a wide range of materials. While stamping often involves lower tooling costs, deep drawing minimizes material waste for intricate shapes, making it a better choice for specific applications.