Deep Draw Stamping Guidelines
Achieving successful deep drawing requires careful attention to multiple factors. Overlooking any one of these elements can lead to challenges in die design and production. However, one principle underpins all others in deep drawing: initiating smooth metal flow. Below are critical factors that influence metal flow, each essential to consider when designing, constructing, or troubleshooting deep drawing stamping dies.
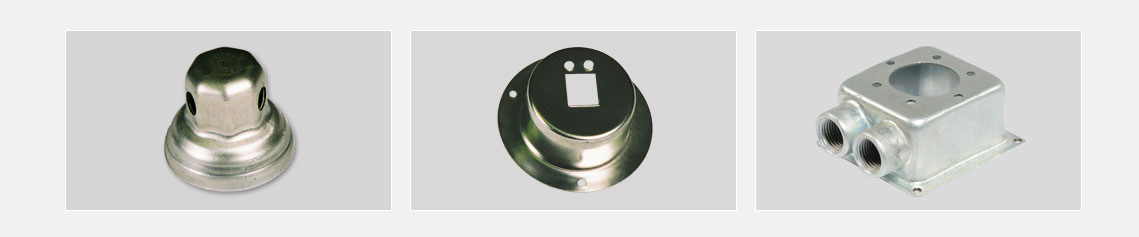
Key Factors Influencing Metal Flow
Material Selection and Thickness
Thicker materials are generally more stable during drawing, allowing them to withstand greater deformation. They also provide more volume, enabling longer stretches without tearing. Select materials that can withstand the necessary strain while maintaining structural integrity.
N and R Values
The N value, or work hardening exponent, indicates how well a metal can stretch, while the R value, or plastic strain ratio, reflects a material’s ability to flow. Both values help determine a material’s suitability for deep drawing by assessing its stretching and flow capabilities.
Blank Size and Shape
Accurate blank sizing and shaping are critical. Blanks that are too large restrict metal flow, while optimized shapes facilitate even material distribution, preventing wrinkling or tearing.
Part Geometry and Draw Radii
The design’s geometry and radii influence how the metal flows into the desired shape. Optimal draw radii, which generally align with material thickness, minimize stretching and prevent thinning or fracturing.
Press Speed (Ram Speed)
Press speed must allow enough time for material flow. Excessive speed can cause tearing, especially in materials with high strain rates, so adjusting speed is key to achieving precise, consistent results.
Die Surface Finish and Lubrication
A polished die surface reduces friction, while the appropriate lubricant enables smoother material sliding. Die temperature affects lubricant viscosity, so both elements should be managed for consistent flow.
Draw Bead Shape and Binder Pressure
Draw beads help control metal flow by creating resistance through bending and unbending. Binder pressure holds the material in place, preventing it from moving too quickly and ensuring even flow through the die.
Optimizing Draw Ratios and Entry Radii
For round draws, the draw ratio—the relationship between the post size and blank size—must remain within acceptable limits. An improper ratio can cause excessive stretching or fracturing. Maintaining an ideal die entry radius further ensures material flows smoothly. Too small a radius increases tearing risk, while an overly large radius in thin materials may lead to wrinkling.
For parts requiring deep draws, reducing the draw in multiple stages may be necessary. Draw reductions enable reshaping within safe limits, allowing gradual refinement to achieve the final profile.
Calculating First Draw Dimensions
To determine the post diameter and height for the initial draw, start with the surface area of the final part and calculate a blank diameter. Multiply this diameter by reduction percentages based on material thickness to obtain the dimensions for the first draw post. These calculations ensure sufficient material is available for the final shape.
Managing Die Entry Radii and Binder Pressure
Die entry radii should suit the material’s thickness and type to prevent fractures or excessive wrinkling. Polished, hook-free radii promote smooth material flow, while sturdy tool steel enhances die durability.
Appropriate binder pressure controls material flow during compression. Standoffs, set to about 110% of material thickness, prevent excessive pinching and enable compressive thickening. Insufficient binder pressure may lead to wrinkling, while excessive pressure restricts material flow.
Tips for Square Draws
Square draws add complexity due to the corner compression involved. Increasing the profile radius can reduce compression, allowing deeper draws in a single pass. Using smaller blank sizes, standoffs, and tailored corner reliefs helps prevent wrinkling while balancing flow.
When a square draw requires multiple stages, all necessary material must be available from the first draw. Adjustments in width, length, and profile radius in subsequent draws ensure the part’s geometry remains intact.
Successful Deep Drawing Design
Successful deep drawing hinges on an array of design and production principles. While advancements in die design continue, understanding and managing fundamental metal flow principles are crucial for achieving efficient, high-quality results. Each part requirement is unique, contact our technical staff for specific recommendations for your application.